“硫化”一詞有其歷史性,因起初的tianran橡膠制品用硫磺作交聯(lián)劑進(jìn)行交聯(lián)而得名,隨著橡膠工業(yè)的發(fā)展,現(xiàn)在可以用多種非硫磺交聯(lián)劑進(jìn)行交聯(lián)。因此硫化的更科學(xué)的意義應(yīng)是“交聯(lián)”或“架橋”,即線性高分子通過交聯(lián)作用而形成的網(wǎng)狀高分子的工藝過程,從物性上即是塑性橡膠轉(zhuǎn)化為彈性橡膠或硬質(zhì)橡膠的過程。
橡膠硫化過程的實(shí)質(zhì)是:橡膠分子鏈在化學(xué)的或物理的因素作用下產(chǎn)生化學(xué)交聯(lián)作用,變成空間網(wǎng)狀結(jié)構(gòu)。因此,現(xiàn)在硫化一詞是指包括硫黃在內(nèi)的許多化學(xué)藥品與橡膠產(chǎn)生交聯(lián)作用的過程。
1、硫化反應(yīng)過程分為哪幾個(gè)階段?
大體可分三個(gè)階段:首先階段為誘導(dǎo)階段,在這階段中,首先是硫化劑分子和cujin劑之前反應(yīng)成一種活性更大的中間化合物,然后進(jìn)一步引發(fā)橡膠分子鏈,產(chǎn)生可交聯(lián)的游離基。其次階段為交聯(lián)反應(yīng)階段,即可交聯(lián)的游離基與橡膠分子鏈之前產(chǎn)生連鎖反應(yīng),生成交聯(lián)鍵。第三階段為網(wǎng)構(gòu)成熟階段,在這階段中的前半階段中交聯(lián)反應(yīng)已趨于完成,已形成的交聯(lián)鍵開始發(fā)生重排和裂解等反應(yīng),出現(xiàn)交聯(lián)與裂解的兩種過程,在這階段的后半段,交聯(lián)反應(yīng)已基本停止,隨之而發(fā)生的主要是交聯(lián)鍵重排和熱裂解等的反應(yīng),即得到硫化膠。
2、橡膠的硫化歷程分為哪個(gè)階段?各階段具有何意義?
橡膠的性能隨硫化時(shí)間的增加而變化,橡膠的硫化歷程可分為四個(gè)階段:焦燒階段、熱硫化階段、平坦硫化階段,過硫階段。
3、橡膠硫化時(shí),為什么要加壓?加壓硫化有哪些目的?
當(dāng)膠料硫化時(shí),由于膠料中含有水分蒸發(fā)以及所含的空氣溢出,致使產(chǎn)生一種內(nèi)壓力,這種內(nèi)壓力會(huì)使膠料膨脹而產(chǎn)生氣孔。為了防止這種現(xiàn)象發(fā)生,硫化時(shí)就務(wù)必施加大于膠料內(nèi)壓力的硫化壓力。膠料在硫化時(shí)要求充分流散和充滿模型。要求硫化壓力要足夠高。隨著硫化壓力增大,橡膠滲入布層的深度增加,從而提高橡膠與布層的密著力和制品的耐屈撓性、施加硫化壓力還能提高制品的強(qiáng)度,nai磨耗等性能,使用壽命也得以延長(zhǎng)。
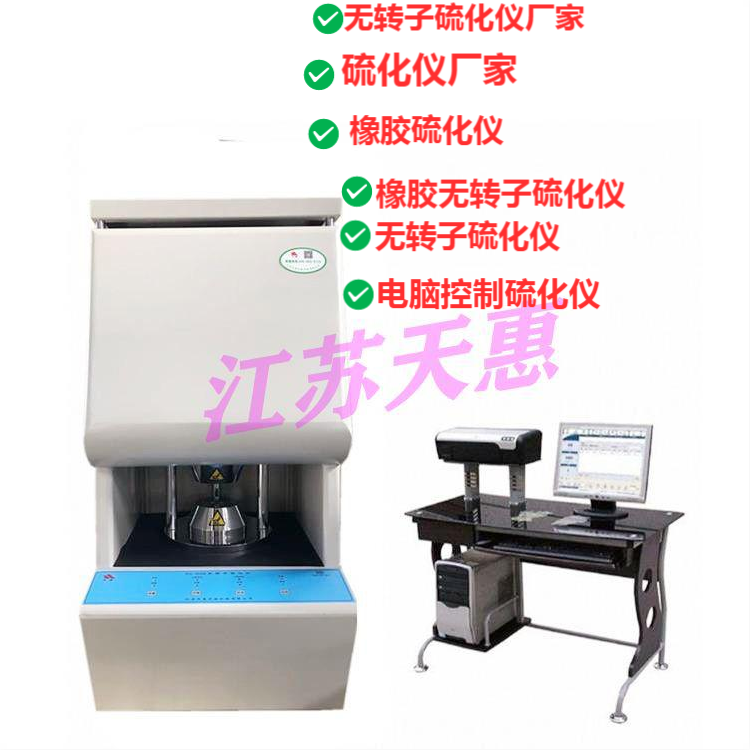
目的概括如下:
1)防止制品在硫化過程中產(chǎn)生氣泡,提高硫化膠的致密性,
2)使膠料流散和充滿模槽,
3)提高橡膠布層的密著度;
4)有助于提高硫化膠的物理機(jī)械性能。
4、硫化壓力的大小對(duì)制品性能有何影響
通常對(duì)硫化壓力的選取應(yīng)根據(jù)膠料的配方,可塑性大小,產(chǎn)品結(jié)構(gòu)等決定,從工藝上考慮,一般原則是:可塑性大,壓力宜小;產(chǎn)品厚,層數(shù)多,結(jié)構(gòu)復(fù)雜,壓力宜大;薄制品壓力宜小甚至可用常壓。
5、硫化中的硫化溫度是否越高越好?
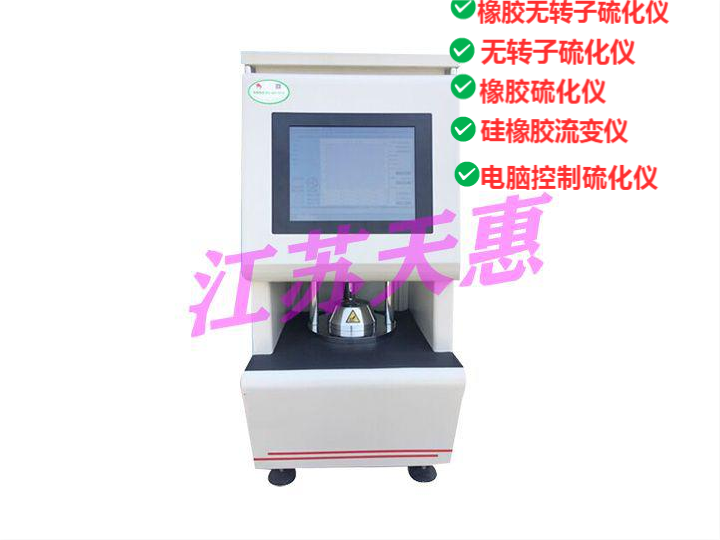
硫化溫度是橡膠硫化反應(yīng)的基本條件,它直接影響硫化速度和產(chǎn)品質(zhì)量,是橡膠硫化工藝中較主要的控制條件之一。
硫化溫度的高低應(yīng)根據(jù)膠料配方而定,其中較重要的是取決于橡膠種類和硫化體系,近年來隨著室溫硫化膠料的增加和高溫硫化的出現(xiàn),硫化溫度趨向兩個(gè)jiduan,特別是高溫硫化引人注目,提高硫化溫度,可以縮短硫化時(shí)間,提高生產(chǎn)效率,但提高硫化溫度要綜合權(quán)衡下列因素;
實(shí)踐表明:各種膠料較宜硫化溫度認(rèn)為是:tianran橡膠<143℃,不超過160℃;丁苯橡膠<180℃,異戊橡膠、順丁橡膠<151℃;氯丁膠<151℃,丁基橡膠<170℃,丁晴橡膠<180℃。
6、硫化溫度和硫化時(shí)間有什么關(guān)系?
硫化溫度和硫化時(shí)間是互相依賴的,
硫化溫度高,硫化速度快,硫化時(shí)間則短;
硫化溫度低,硫化速度慢,硫化時(shí)間則長(zhǎng)。